High-Endurance Cutting Edges
Challenges Revealed in High Magnification
Tough Cutting Edges . . .
- Apex photos & drawings are presented below with annotations to clarify some of the latest research currently shared online.
- Some of the most informative web sites I have found to date . . .
- ScienceOfSharp.com
( Sharpening Photos & Info.)
- www.youtube.com
/@HomeSliceSharpening. . .
( Dual-Grit Sharpening
Info & Video )
-Instagram.com/KnifeSteelNerds
( Knife Steel,
Info. & Videos )
- Optimization of knife steels & associated sharpening methods for best culinary cutting edges is an evolving science.
- These individuals have spent countless hours & resources to develop outstanding knife steels and sharpening methods.
- High magnification images of knife steels & cutting edges, created using various sharpening methods, are very revealing.
- People generously share their knowledge.
- Please:
Like,
Comment,
Support,
Share & Subscribe. . .
to support their generosity.
Knife - Apex Photos
Steel Damage - Cracks Highlighted
Innovative - Wet Slurry - Abrasive Sharpening
- Sharpened on a wet stone with a wet abrasive slurry.
- The slurry of abrasive grit & water, grinds away the softer elements of steel.
- Harder carbides populate the cutting-edge surface.
- A carbide-rich cutting edge reduces wear, improving edge retention.
- The wet slurry reduces abrasion-related blade surface heat buildup.
- Steel surface carbon cracking is minimal ( 0.3 Micron ).
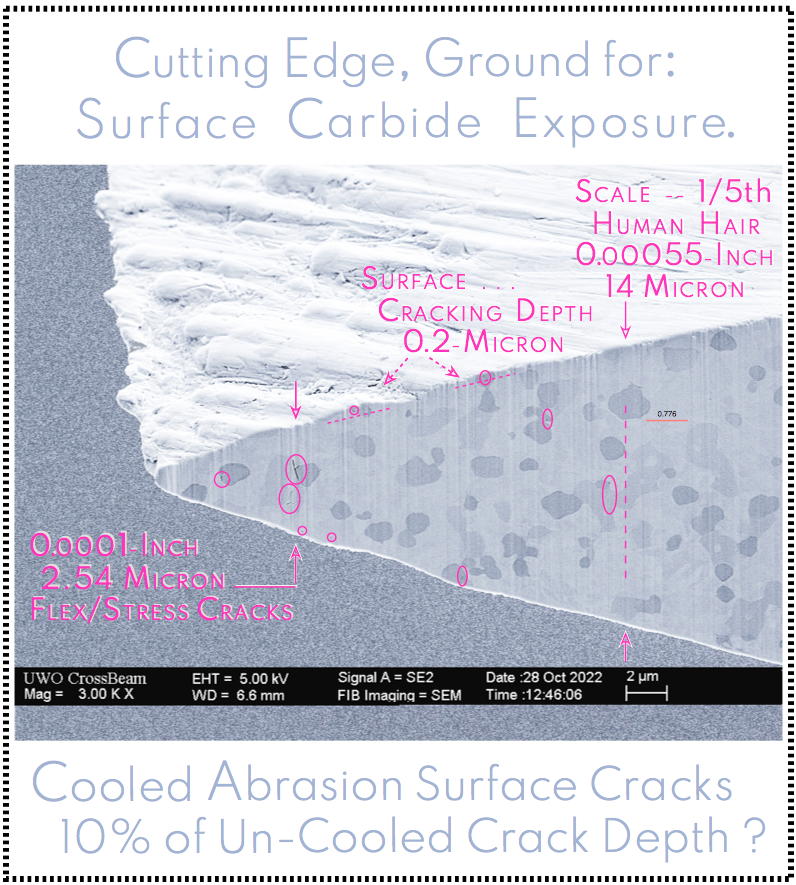
Classic - Apex Grind
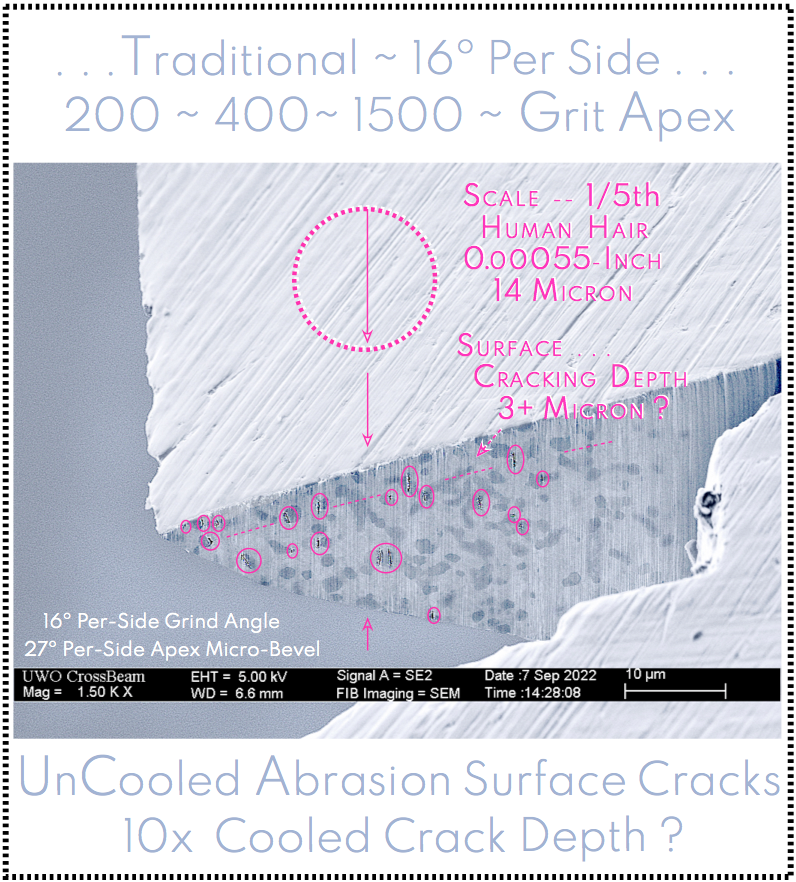
Traditional, Dry-Hand ...
Sharpening Methods
- Sharpened with/on high-quality DMT diamond plates.
- This process yields minimal damage to the knife steel from abrasion-related heat & stress/flex.
- However, heat-related carbon cracking still seems to exist to a depth of 3 Microns.
- Additional cracking from steel flexing near the apex appears to be present at greater depths.
- Dry hand sharpening methods reduce steel damage by 90+% over many dry high-speed abrasive sharpening methods.
Cutting
Edge -
Burrs
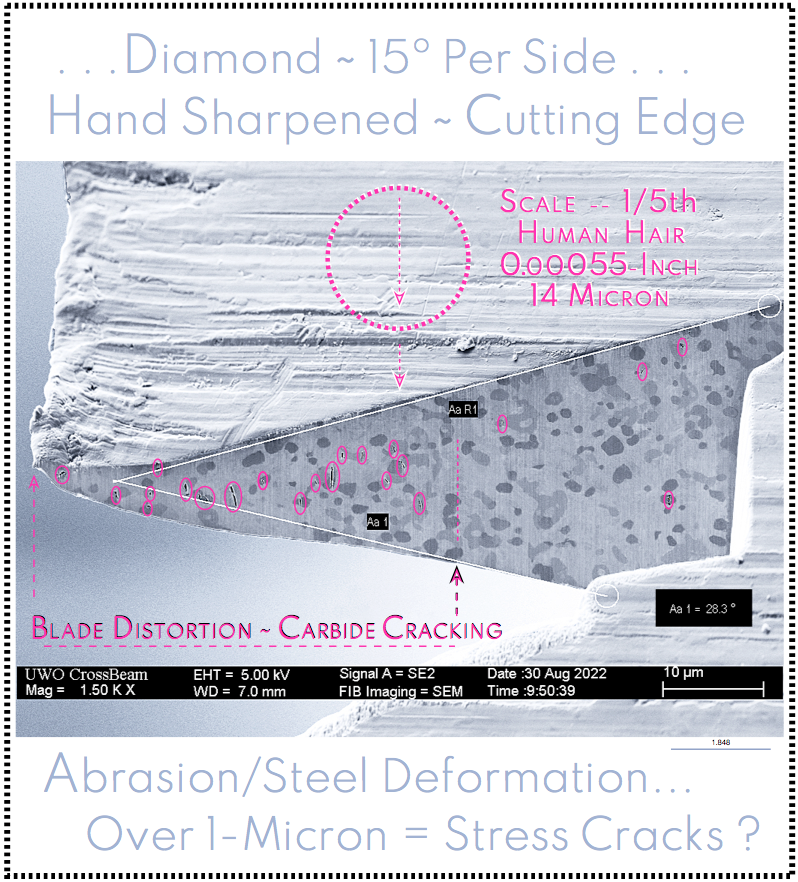
Steel Distortion . . .
Increases Carbide Cracking
- Photo depicts a significant increase in carbon cracking at 0.5 Micron distortion levels . . .
- Increased cracking correlates with areas of steel distortion in the apex.
- Knife blade distortion exists in 17 Micron & thinner portions of cutting edge.
- Carbon cracking is prevalent in 15 Micron & thinner cross-sectional areas.
- Carbon cracking increases in 2.5 Micron & thinner flexed blade steel.
- Cracks deteriorate cutting-edge strength & durability.
- Steeling a cutting edge has the effect of distorting the apex over & over again.
- This process has
minimal short-term
value with
negative long-term
effects.
Apex - Surface
Cracking
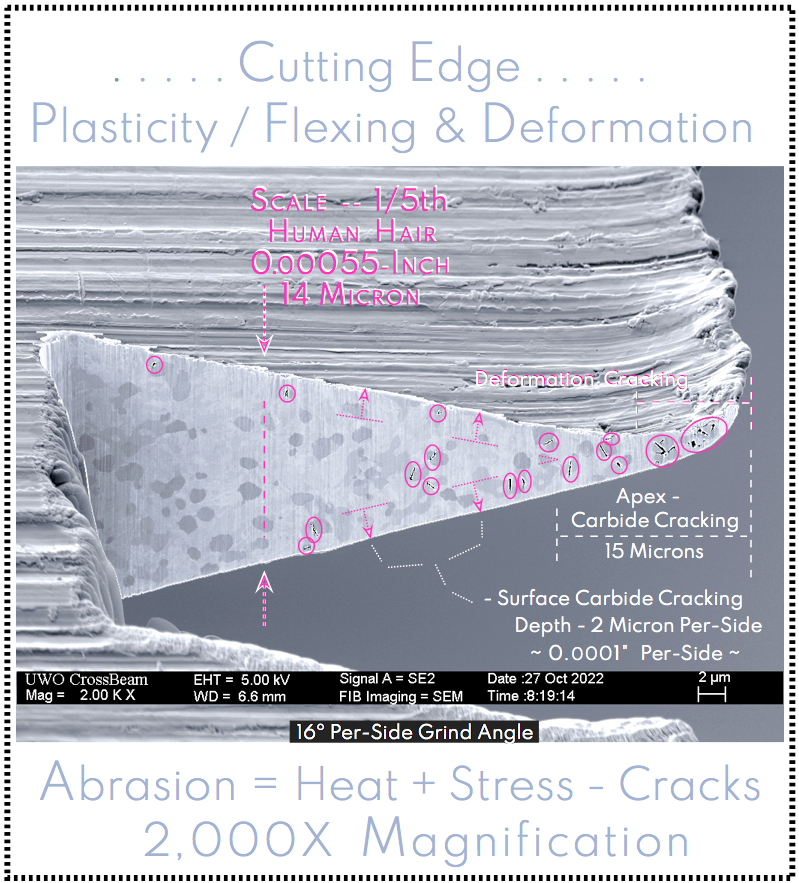
Heat/Stress . . .
Carbide Cracking
- Photo depicts a hand sharpened with high-quality dry diamond plates.
- This dry process creates minimal heat & stress/flex in the knife steel.
- However, heat-related carbon cracking seems to exist to a depth of 2 Microns.
- Additional cracking from steel flexing near the apex seems to exist at 4 Micron.
- Increased levels of carbon cracking are visible in the deformed portion of the apex.
- Low angle small diameter cutting edges often chip out and/or roll over with minimal use.
- Micrographs seem to confirm, cutting-edges with radiuses below 2 Microns have stability issues.
Knife Burr - Cracking
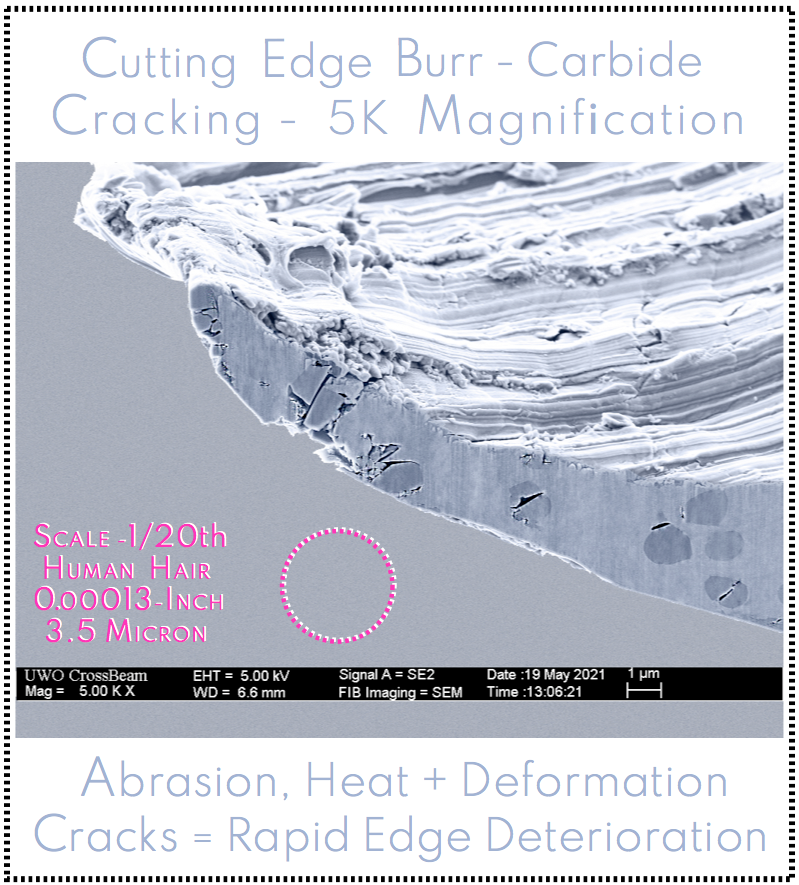
High Carbon Knife Steel
Apex/Burr Distortion
- Close examination reveals widespread cracking in the cutting edge.
- Cracks are visible on the surface & also revealed in the cross-section.
- Cutting edges, with cross-sectional areas of knife steel, less than 2 Micron, often roll over &/or chip out.
- The cutting edge depicted is likely hand sharpened on diamond plates, yielding relatively low levels of carbon cracking.
- High abrasive speed/pressure sharpening systems will yield more heat-related steel deterioration.
- Abrasion related heat/knife steel testing reveals 4 to 5 HRC point reductions.
- Wear resistance reduction calculation is a 5% per-point loss of HRC.
Hi-Magnification - Apex Cracking
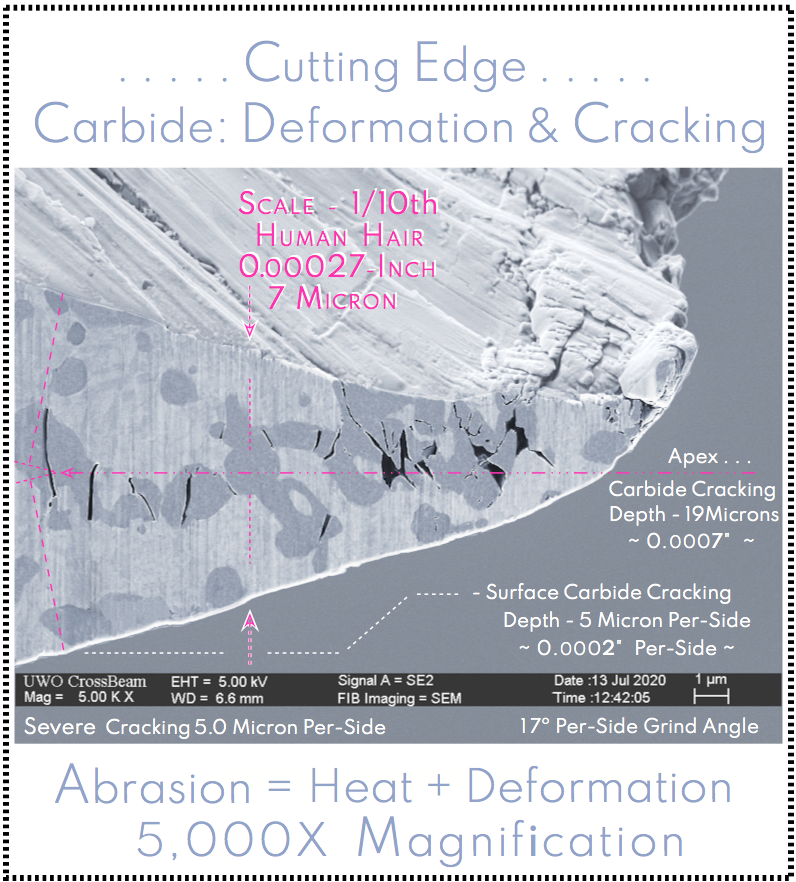
Carbon Clumping &
Carbide Cracking...
- This image reveals severe carbon cracking across large carbon structures.
- With minimal use, the cutting edge will likely chip out, yielding a cutting edge radius of 3 Microns.
- The cutting edge depicted in this micrograph would yield razor sharp test results.
- Cutting edge durability would be less than ideal.
- Ideally, knife steel is balanced to provide hardness for long wear & toughness to avoid chipping out.
- The ideal balance depends upon user skill levels & foods they are cutting.
Micro - Chipped Apex
High Carbon Steel
Cracked/Chipped Apex
- This micrograph depicts a knife steel too hard for the intended use.
- Ideally, we trade off a bit of hardness for toughness.
- A 32º micro apex grind will increase apex stability & cutting performance.
- 32º plus apex grinds also perform well on softer knife steels, which often roll over.
- Stropping a 17º apex can easily yield a 25º to 30º micro apex.
- Avoiding heat build-up in knife steels during the sharpening process increases the durability of a cutting edge.
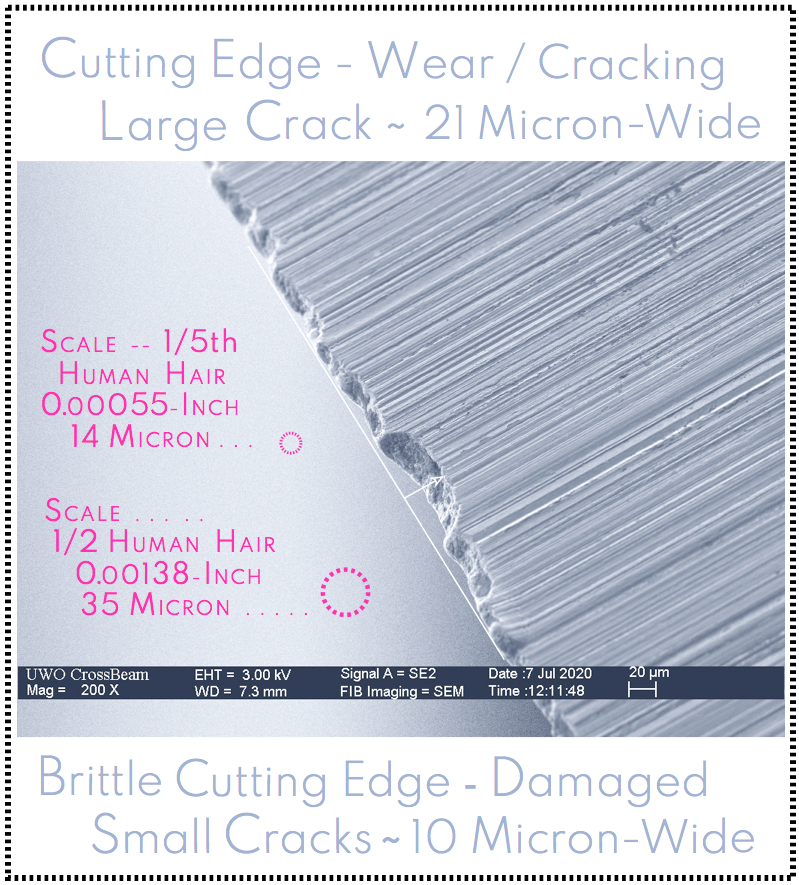
Knife Blades - Apex Wear
High-Endurance Cutting Edge
Dual Grit Sharpening,
High Performance

Cross-Section, Perspective
High-Magnification Cutting Edge View
Dual Grit Cutting Edge
- Cross-sectional view along the cutting edge/apex of a dual-grit sharpened knife blade before stropping.
- A burr is formed when steel cannot withstand the pressure necessary to abrade/grind it away.
- This image reveals a relatively large burr.
- This is metal forced outside the triangle... of the expected sharpening angles.
- A smaller burr is attached to the larger burr at the apex.
- This cutting edge was created using a dual grit sharpening method with edge trailing strokes.
- A 250-grit diamond plate and a 1,000-grit water stone were used to create this cutting edge.
Dual Grit - Apex Photos
Course & Fine - Apex Side Views
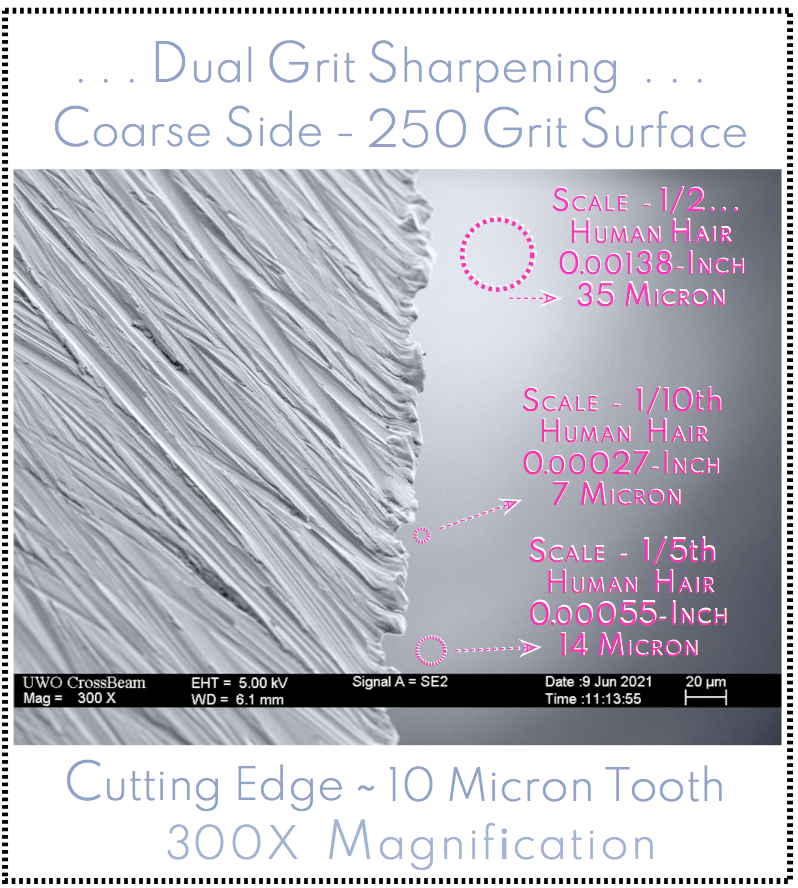
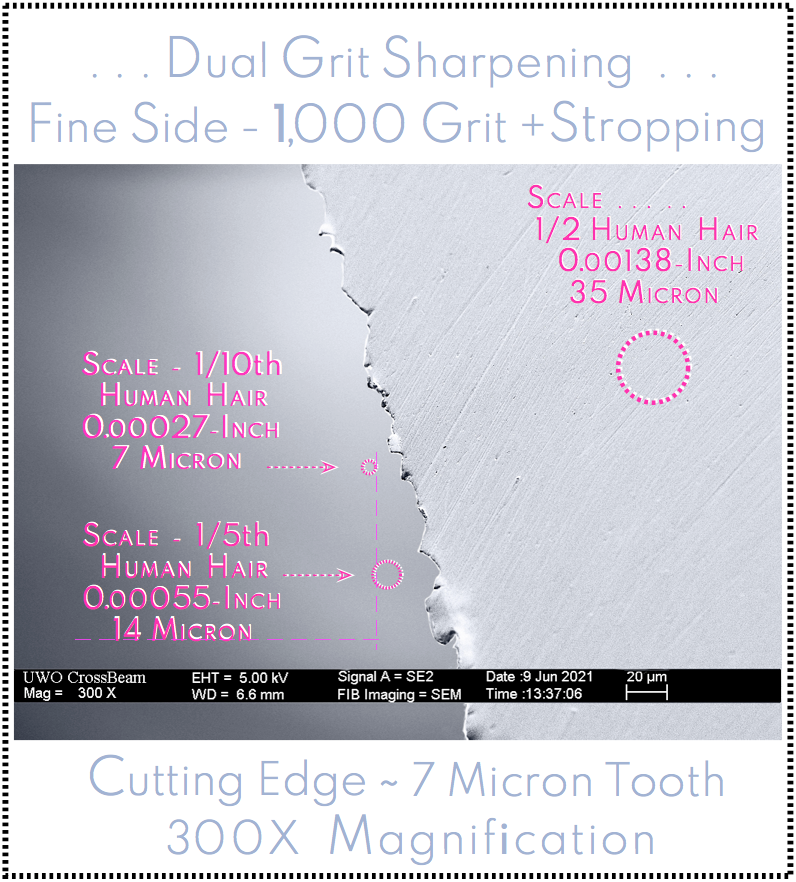
Higher Abrasive Speeds
Test Data ~ Thoughts & Comparisons
High-Speed Sharpening
- Test data reveals significant HRC reduction in the cutting edge sharpened with high-speed abrasives.
- HRC deterioration depth: 100 Micron (0.004") behind the apex ... 38 Micron (0.0015") per side ... in this example.
- 90+% of this damage is avoidable using cooled and/or low surface speed/pressure abrasives.
- High-quality knife steel cutting edge durability is often reduced to that expected of low-quality knife steel.
- Mass-produced knives are often sharpened with high surface speed abrasives.
- These sharpening systems produce incredibly sharp, reduced durability cutting edges.
- Wet/cooled & lower speed/pressure sharpening processes reduce heat & improve HRC retention in the cutting edge.
- Resharpening a knife on a diamond plate or wet stone several times, often increases cutting-edge durability.
- This test data & diagram correlates well with my personal research & other test data shared on the internet.
Cutting Edge- HRC Issues
High Abrasive Speeds = High HRC Loss
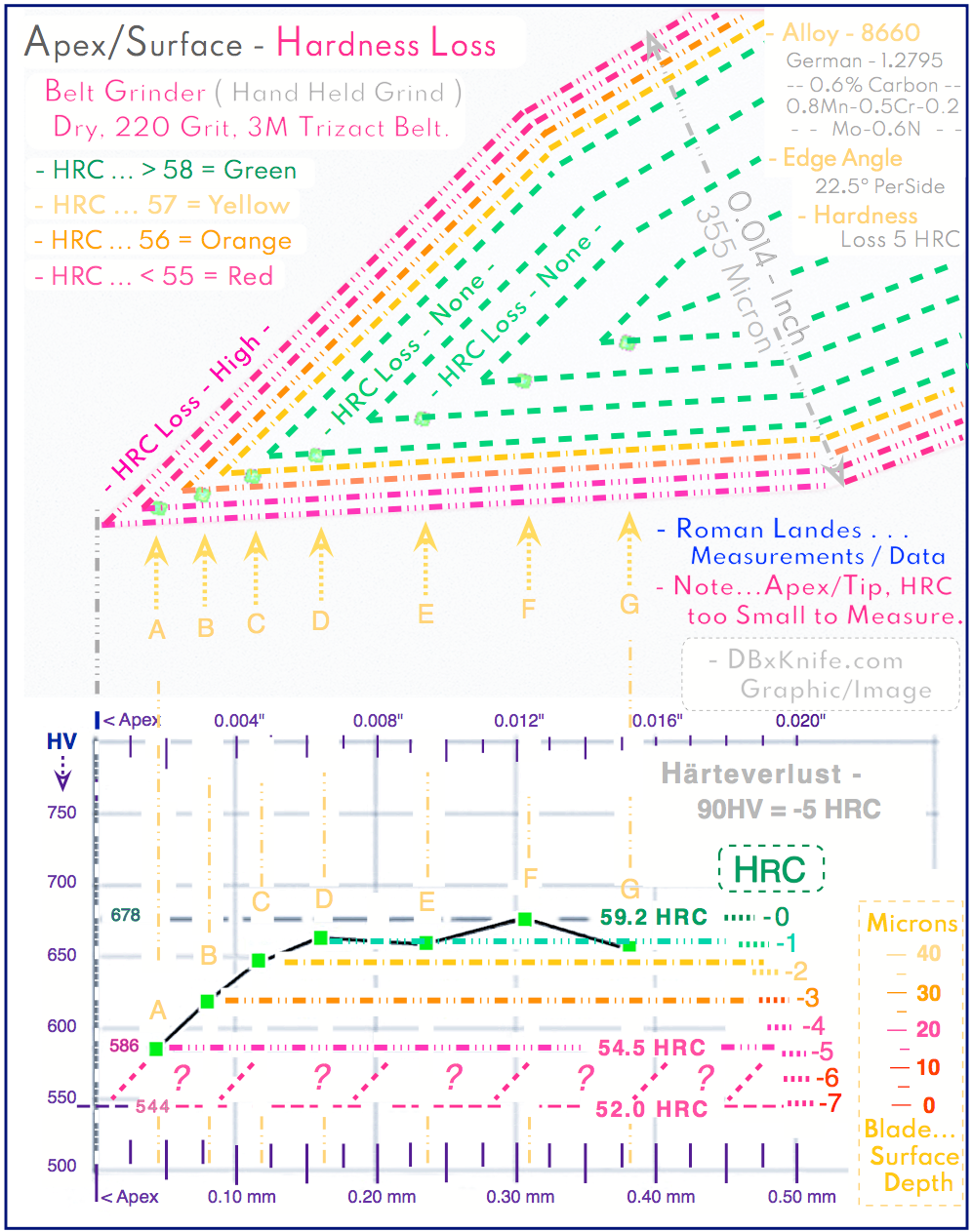